Understanding the Specifications and Internal Structure of Cat6 Cables
Overview of Cat6 Cables:
Cat6, which stands for Category 6, is a standardized Ethernet and network cable used for high-speed gigabit networks. These cables are an improvement over their predecessor, the Cat5e cables.
What Makes Them Special?
- Higher Bandwidth: Cat6 cables can support up to 10 Gbps speeds up to 164 feet. This higher bandwidth ensures they can handle more network traffic and support more simultaneous high-speed connections.
- Reduced Crosstalk: With an improved internal design, Cat6 reduces crosstalk, which refers to the interference you can sometimes hear between channels in a communication cable. This leads to more precise and more reliable data transmission.
- Versatility: While designed for gigabit Ethernet, they are backwards compatible with Cat5e, Cat5, and even Cat3 standards.
Their Importance in Data Transmission:
In today’s age of data-heavy applications, streaming services, online gaming, and digital enterprises, the need for a fast and reliable internet connection has never been more critical. Cat6 cables are at the forefront, providing a backbone for high-speed networks in homes and businesses.
Analyzing the Internal Structure:
Twisted Pairs: Cat6 cables typically come with four pairs of copper wires, making a total of eight wires. These pairs are twisted together, and each twist rate varies to help reduce interference from both internal and external sources.
Separator: A unique feature in many Cat6 cables is a longitudinal separator. This separator isolates each of the four pairs of twisted wire from each other, resulting in reduced crosstalk, improved signal isolation, and enhanced performance.
Material Composition:
The primary material in Cat6 cables is high-quality copper, known for its excellent conductivity. This high-grade copper ensures efficient data transmission with minimal loss.
Insulation: Each of the eight wires in the cable is individually insulated, often with a material called high-density polyethylene (HDPE). This insulation protects the inner copper wire and helps prevent electrical interference that might degrade the signal.
Outer Jacket: An outer jacket, typically made of PVC or LSZH (Low Smoke Zero Halogen) material, protects all these internal components. This jacket provides physical protection and can come in various colors for easy identification during installation.
Significance in Ensuring Quality and Durability:
Quality materials are paramount in achieving the high performance that Cat6 cables promise. High-grade copper ensures maximum conductivity and minimal signal loss. The choice of insulation and jacket materials protects the cable from external elements, wear, and tear, ensuring longevity and consistent performance.
Machinery and Detailed Production Process
Wire Drawing Machine:
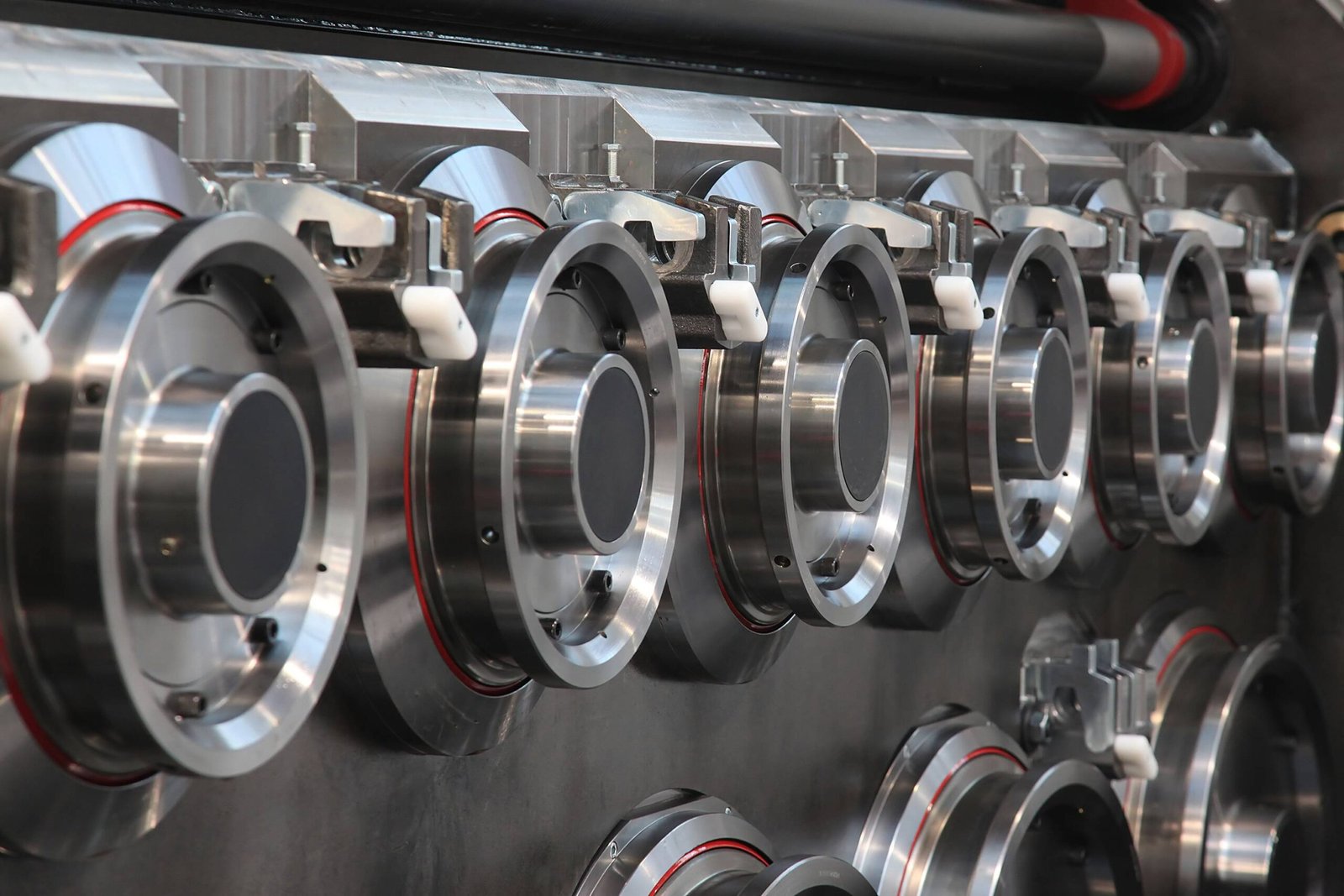
The first step in producing Cat6 cables involves converting raw copper into thin wires.
How It Works:
- Raw Material: The process begins with large rods or coils of bare copper.
- Drawing Process: These copper rods are fed into the wire drawing machine, which uses a series of dies (typically made of diamond or tungsten) to reduce the copper’s diameter progressively. As the copper is pulled through each die, it becomes thinner and longer.
- Heat Treatment: After drawing, the wire undergoes a heat treatment process called annealing. This softens the wire, making it more flexible, which is crucial for its subsequent cable coiling and usage.
Importance of Precision: The precision in this process is paramount. Any wire thickness inconsistencies can lead to performance issues in the final product. Precise wire drawing ensures uniform electrical conductivity and strength across the entire length of the wire.
Insulation Extrusion Machine:
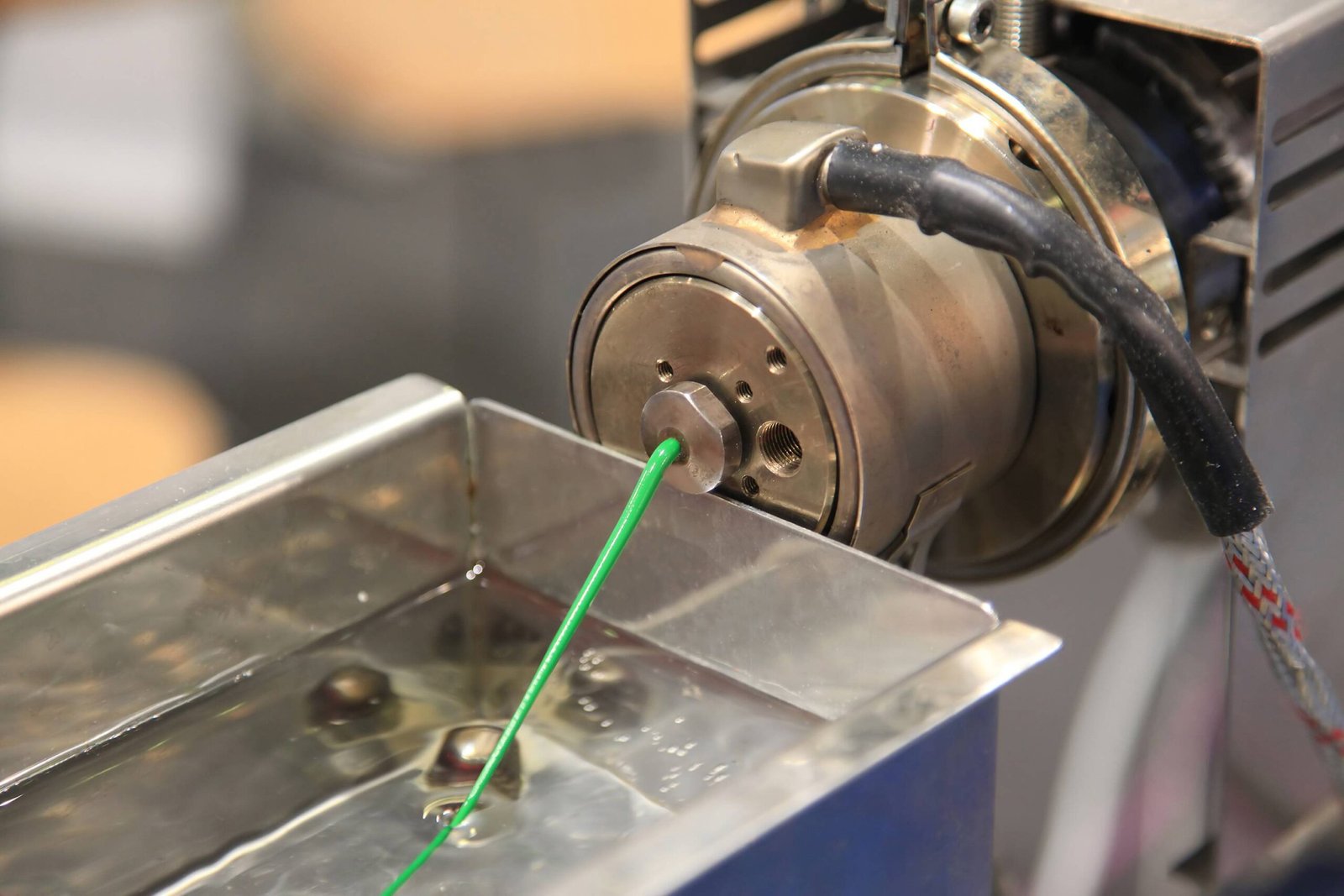
Once the copper wire is drawn, it must be insulated to protect it from external elements and ensure effective data transmission.
The Process:
- Feeding the Wire: The drawn copper wire is fed into the extrusion machine.
- Extrusion: As the wire moves through the device, it’s surrounded by a material (often high-density polyethylene or HDPE), which is then heated until it becomes semi-liquid. This material is extruded around the wire, forming a protective layer.
- Cooling: The insulated wire is cooled rapidly, solidifying the insulation layer.
Twisting Machines:
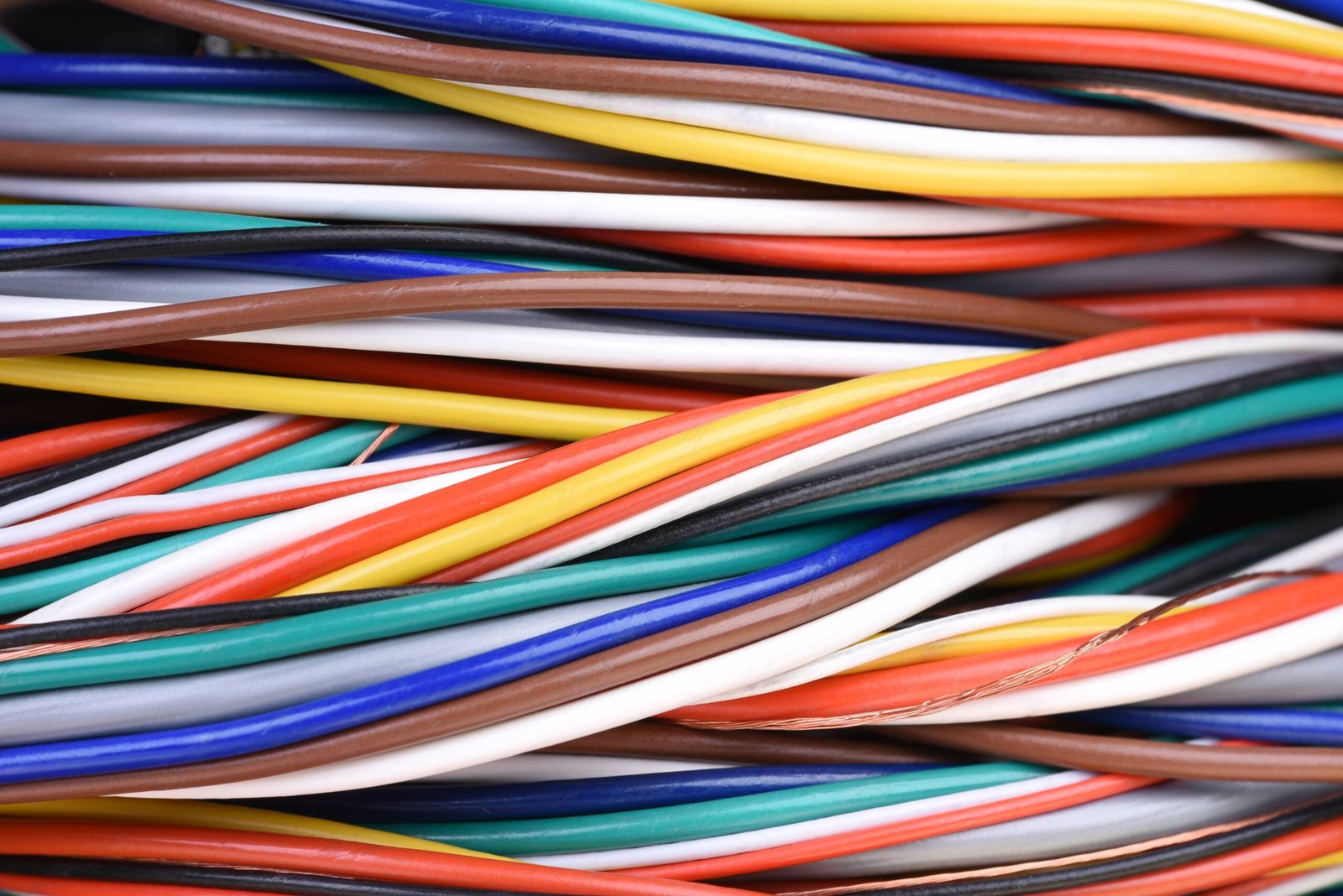
The insulation-encased wires are then twisted into pairs. This is a crucial step, as the twist rate (or the number of twists per meter) can significantly affect the cable’s performance.
Twisting to Reduce Interference: The main reason behind the twisting is to reduce electromagnetic interference (EMI) from internal and external sources. By having two wires carry signals and twisting them, the other cancels any interference affecting one wire.
Stranding Machines:
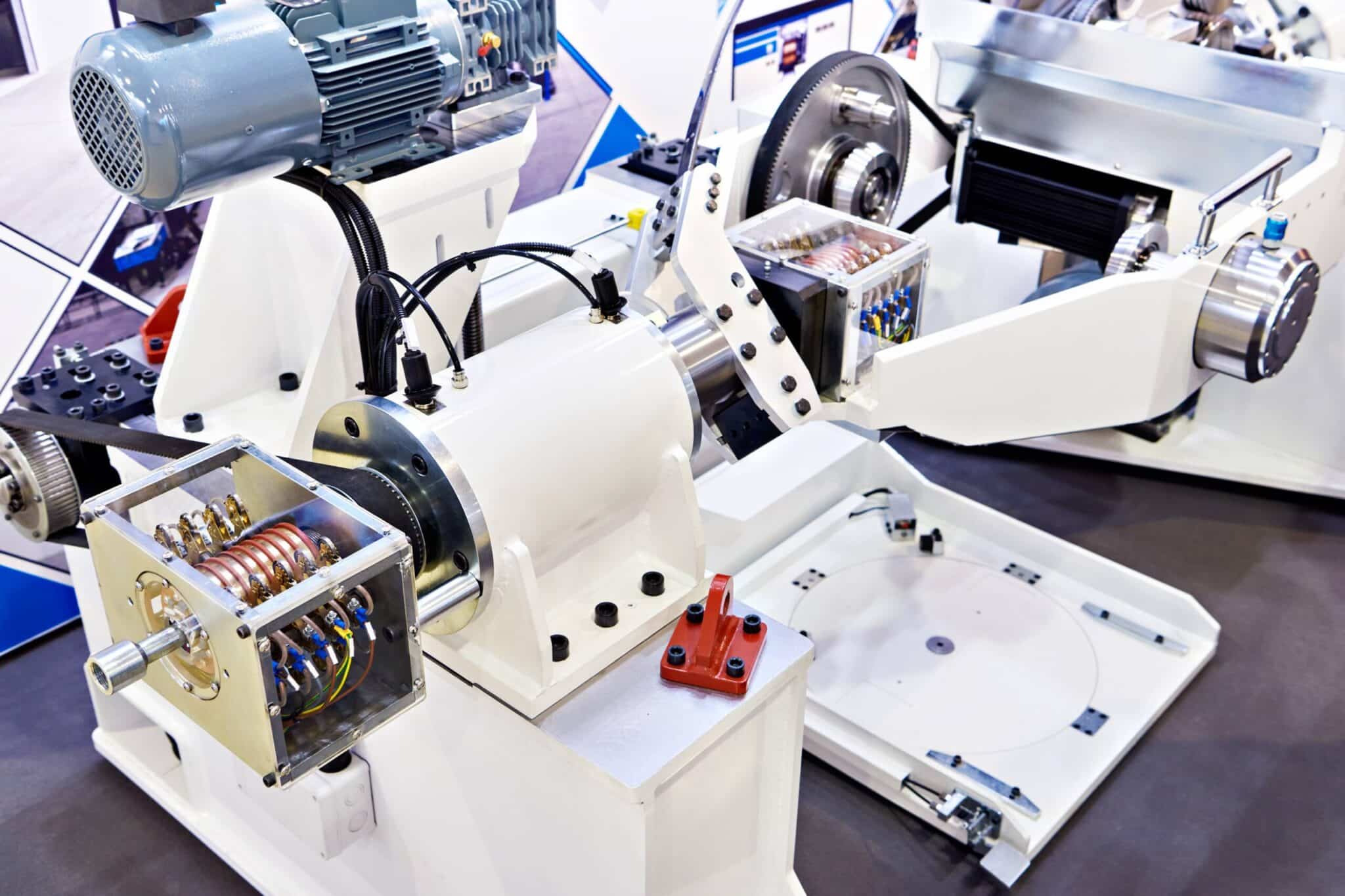
After twisting, the pairs are combined using cabling machines.
The Process:
- Feeding: The twisted pairs are fed into the cabling machine.
- Combining: They are laid together in a specific configuration, ensuring they remain in order and untangled.
- Stranding: One way to improve the strength of a cable is by adding a central strength member, around which the twisted pairs can be stranded.
Sheathing Machines:
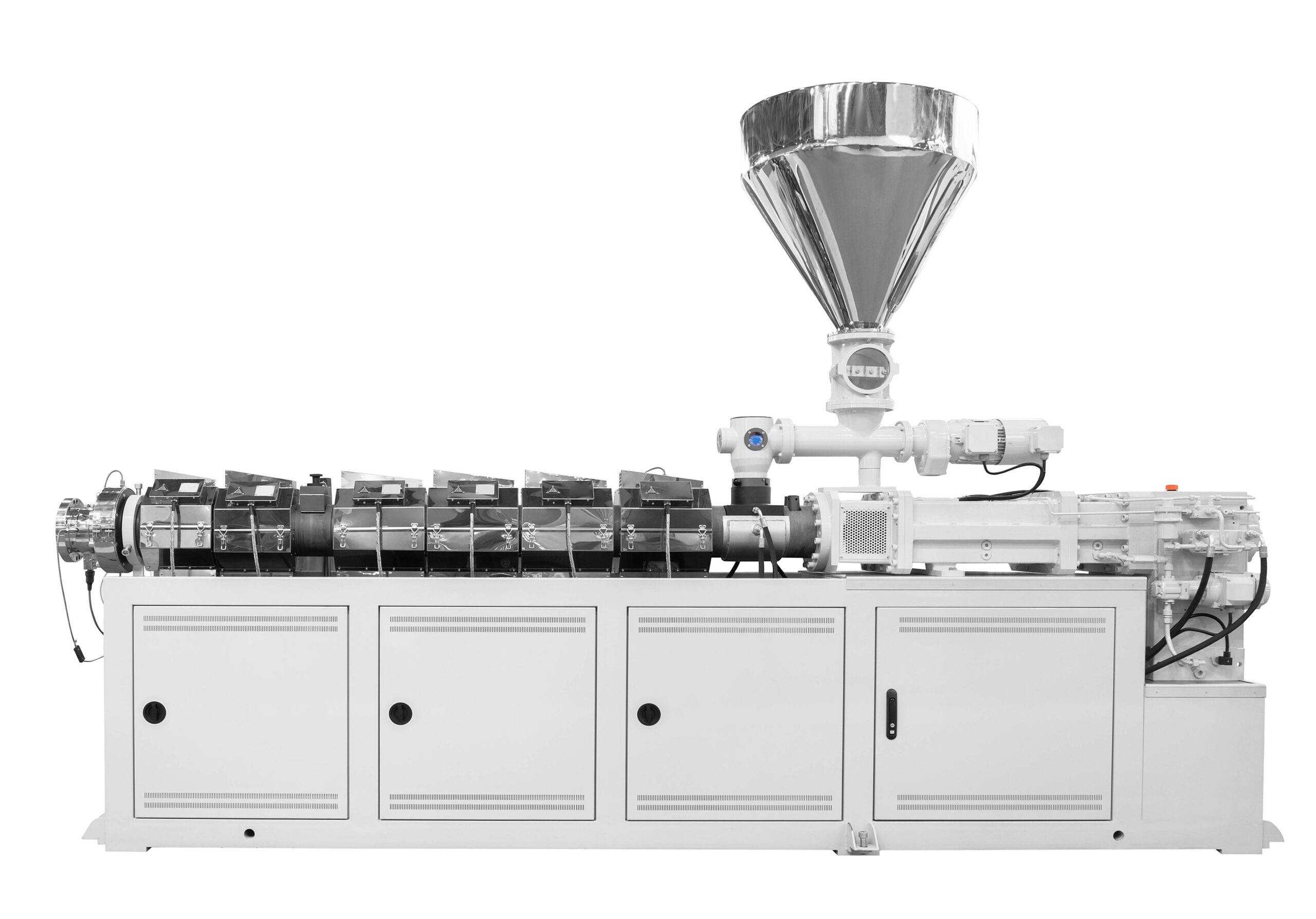
The final step in the production process is the addition of the outer protective layer or the sheath.
How It Works:
- Feeding: The combined twisted pairs (now essentially forming the core of the cable) are fed into the sheathing machine.
- Extrusion: Similar to the insulation extrusion process, a material (usually PVC or LSZH) is heated and extruded around the cable core.
- Cooling and Coiling: The cable is cooled after sheathing, solidifying the outer layer. It’s then coiled or wound onto reels, ready for testing and eventual deployment.
Precautions in the Production Process
Ensuring Consistency:
In the world of cable manufacturing, consistency is the name of the game. Every inch of the Cat6 cable must meet the same high standards, ensuring optimal performance throughout its length.
Why It’s Vital:
- Performance Reliability: A consistent cable guarantees uniform transmission rates, ensuring the user doesn’t experience sporadic drops in data speeds.
- Durability: Uniformity ensures that no section of the cable is weaker than others, leading to a longer lifespan.
Achieving Consistency:
- Regular Checks: The production line should have frequent checkpoints to examine the cable’s thickness, insulation, and other properties.
- Calibration: Machines used in production, like extruders and twisting machines, should be frequently calibrated to maintain accuracy.
Avoiding Contaminants:
Even the tiniest speck of dust can be a villain in the production of Cat6 cables.
The Risks:
- Material Degradation: Contaminants can degrade the insulation material, affecting its protective properties.
- Performance Impact: Foreign particles can lead to electrical interference, compromising data transmission quality.
Prevention Measures:
- Clean Environment: Regular cleaning of the production area and equipping airflow systems with filters to prevent dust entry are essential.
- Protective Gear: Workers should wear protective clothing, including hairnets and gloves, to avoid human-origin contaminants.
Temperature and Humidity Control:
Producing cables under certain conditions significantly impacts their quality.
Why It’s Important:
- Material Behavior: The copper used for the wires, and the plastic used for insulation can behave differently under varying temperatures. Proper temperature ensures they remain in their optimal state during production.
- Humidity Impact: Excess moisture can affect the insulation’s adherence to the copper and, in extreme cases, cause internal condensation, deleting the cable’s performance over time.
Maintaining Optimal Conditions:
- Climate Control: The production area should have HVAC systems to stabilize temperature and humidity.
- Regular Monitoring: Continuously monitor environmental conditions and trigger alarms for any significant deviations to facilitate prompt adjustments.
Raw Materials, Testing, and Grading
Selection of Raw Materials:
Hey there, future cable master! Let’s get one thing straight – the foundation of a robust Cat6 cable lies in picking the best raw materials. So, what’s the secret sauce?
- Quality Copper: We always go for the highest grade copper. Why? Premium copper ensures efficient data transmission, reducing potential lags or interference. We’re talking about that smooth streaming experience you love!
- Top-Notch Insulation: The insulation isn’t just there for the looks; it’s the protective shield of our cables. By choosing only the best insulation materials, we ensure our cables remain safe, durable, and ready for action, even in challenging conditions.
Standard Tests for Cat6 Cables:
Testing is like the gym session for our cables; it keeps them fit and in top shape! Before they hit the shelves, our cables flex their muscles through a series of tests:
- Signal Strength Test: We ensure data zips through our cables without hitches, giving you a seamless online experience.
- Durability Test: We put our cables through the wringer from bends to stretches. We ensure they’re not just strong but also agile!
- Performance Metrics: Speed matters, right? That’s why we constantly check if our cables are running at their best speed, ensuring you get top-tier performance daily.
Grading the Cables:
Before considering grading, we must know what tests and standards these cables have passed. In the cable testing world, strict guidelines and parameters are set to ensure only the highest quality cables reach your devices.
The Test Standards:
- Propagation Delay: This is about measuring the time it takes for a signal to travel from one end of the cable to the other. The delay must be minimal for a seamless experience, especially during intense gaming sessions or video calls.
- Return Loss: We’re looking at the reflection of signals in the cable. A higher return loss indicates a clearer, better-quality signal.
- Insertion Loss (or Attenuation): This evaluates how much the signal weakens as it travels down the cable. The less the loss, the better the cable quality.
- Near-End Crosstalk (NEXT): Here, we measure interference. We want to ensure that signals in one wire don’t interfere with those in another.
- Far-End Crosstalk (FEXT): Similar to NEXT, this evaluates interference at the far end of the cable.
- Alien Crosstalk: This one’s interesting. It measures the interference from signals in adjacent cables. Yes, we’re that thorough!
Now, let’s break down the grades:
- Grade A: These are our star performers, acing every test and setting benchmarks. If you’re looking for the best of the best, this is where your search ends!
- Grade B: Don’t be fooled; these cables are still fantastic. They perform exceptionally well and are ideal for most standard applications.
- Grade C: They might not be the valedictorians, but they’re reliable, sturdy, and offer great value for your buck.
Handpicking Your Perfect Supplier
Factors to Consider:
Now, we’re going to select suppliers off the street. We’ll be picky because, well, we should be. Here’s our game plan:
- Quality Assurance: Always, always prioritize quality. Ask for certifications, standards met, and any other badges of honor they’ve earned. We’re investing money; we deserve the best!
- Past Track Record: A supplier’s history can tell us heaps. Dive into those customer reviews, testimonials, and case studies. We want someone who has wowed their customers time and time again.
- Technical Expertise: Let’s get nerdy and talk tech! Your supplier should be equipped with the latest machinery, up-to-date with industry standards, and be a cable wizard.
Negotiating the Best Deal:
Ah, the art of negotiation. We’re not just aiming for the cheapest – we want the best value. Discuss volume discounts, payment terms, or any other perks they might throw in. Remember, it’s not just about cost but getting a bang for our buck!
Building Long-term Relationships:
Here’s the golden nugget – finding a supplier isn’t a one-off thing. We’re in it for the long haul. A consistent, reliable supplier is like that old friend who’s always there when you need them. The advantages? Smooth communication, special deals, and the comforting knowledge that we’re in capable hands.
Wrapping It All Up!
We’ve journeyed through the intricacies of Cat6 cables, from their core to their production. It’s fascinating stuff.
The world of cable production is ever-evolving. As we strive for perfection, we also eagerly anticipate the next big thing in this field.
Are you eager to dive deeper? Have you got questions? Reach out or click here for more. Let’s continue exploring this vast world together! Cheers to more discoveries! 🚀
FAQ
- What is a Cat6 cable?
- Cat6, standing for Category 6, is a standardized network cable designed for high-speed gigabit networks, offering improved performance over its predecessor, Cat5e.
- Why are Cat6 cables faster and more reliable?
- Cat6 cables support up to 10 Gbps speeds and are designed with reduced crosstalk and interference, ensuring precise and consistent data transmission.
- Are Cat6 cables compatible with older cable versions?
- Yes, Cat6 cables are backward compatible with Cat5e, Cat5, and Cat3 standards.
- What is the internal structure of a Cat6 cable?
- It contains four twisted pairs of copper wires (a total of eight wires). A unique feature in many Cat6 cables is a longitudinal separator that isolates each wire pair for reduced interference.
- Why is the production process of Cat6 cables so intricate?
- Consistency in production ensures optimal performance and durability. The precision in wire drawing, insulation, and twisting is paramount for high-quality and consistent data transmission.
- How are Cat6 cables tested for quality?
- They undergo tests for signal strength, durability, speed, and interference (like Near-End and Far-End Crosstalk) to ensure top-tier performance and reliability.