O que é Patch-Cord/Soft Cable?
Pela estrutura abaixo, pode-se observar visualmente que sua estrutura consiste nas seguintes partes:
- Fibra
- Fio
- Bainha LSZH
Então, se analisarmos de acordo com nossos artigos anteriores: Como escolher uma linha de produção de acordo com os diferentes cabos ópticos, Isso é feito pelas seguintes máquinas:
Como fazer o cabo drop FTTH por máquinas?
1. Torre de desenho
O núcleo e o revestimento da fibra óptica são feitos de vidro de sílica altamente purificado. As fibras ópticas são feitas de sílica de duas maneiras. O primeiro método é o método do cadinho. Neste método, o pó de silício é derretido para produzir uma fibra multimodo mais espessa, que é adequada para a transmissão de curta distância de muitos sinais de ondas de luz. O segundo método, deposição de vapor, produz um cilindro sólido composto por um material de núcleo e um material de revestimento, que é então aquecido e puxado para uma fibra óptica monomodo mais fina para comunicação de longa distância.
Especificação da Torre de Desenho
- Módulo de alimentação de pré-formas
- Forno
- Montagem do trator de partida
- Sistema de fornecimento de gás (para argônio)
- Filtros HEPA
- Medição do diâmetro da fibra
- Sistema de revestimento de fibra
- Fornos de cura UV e térmica
- Medição do diâmetro do revestimento
- Controle de centralização de fibra
- Controle de concentricidade do revestimento de fibra
- Medição de tensão de fibra
- Extrator de cabrestante / fibra
- Enrolador de fibra/trocador de tambor
- Testador/rebobinador à prova de fibra
1. Módulo de alimentação de pré-formas: As pré-formas são colocadas num forno. A velocidade e o posicionamento das pré-formas são controlados para que fiquem no meio do forno. A velocidade com que as pré-formas descem para o forno é definida pela rapidez com que o fio está sendo trefilado, pelo tamanho da pré-forma e pela espessura desejada da fibra.
O diâmetro da fibra é ajustado pela rapidez com que o fio está sendo trefilado. A tensão de alongamento é controlada pela temperatura do forno. Essa tensão precisa ser monitorada e mantida constante durante a trefilação para que as fibras não fiquem muito apertadas ou muito soltas.
2. Forno: A pré-forma é colocada em um orifício na parte superior do forno. O forno é cilíndrico e possui eixo vertical. Na superfície inferior existe um orifício de onde saem fibras de pequeno diâmetro. Ambos os furos possuem íris para alterar o diâmetro, permitindo ao operador controlar o fluxo de gás no forno.
O forno usa um elemento elétrico de alta tensão – geralmente uma unidade de resistência de grafite. Para iniciar a trefilação, a pré-forma é colocada no forno. A zona de trefilação é aquecida acima de 1900°C, onde o vidro amolece e estica, e as gotas de água puxam as fibras.
3. Montagem do trator de partida: A água que escorre abaixo da fornalha é cortada. A fibra então passa por um trator de duas rodas que a puxa para baixo. O diâmetro da fibra é reduzido até atingir a especificação correta.
Em seguida, as fibras entram em um sistema de revestimento e seguem uma torre até o fundo. Lá, um guincho assume o controle e os puxa para baixo. Depois disso, o guincho na parte inferior controla a rapidez com que as fibras são estiradas com base em um circuito de feedback com um medidor de diâmetro.
4. Fornecimento de gás para o forno: O forno está muito quente, em torno de 2.000°C. Mas se a temperatura ficar muito alta, acima de 600 a 800°C, o grafite começará a se decompor e a criar poluição.
Para evitar isso, o argônio é usado para ajudar a controlar a temperatura. O argônio também ajuda a interromper a turbulência no ar que pode causar danos. À medida que o argônio flui pelo forno, usamos uma íris para controlar a quantidade que entra e sai. É importante manter o fluxo de argônio exatamente correto, por isso usamos diferentes técnicas para fazer isso.
5. Filtragem de ar: A lenta velocidade de estiragem usada para fibras especiais significa que as fibras não revestidas são geralmente resfriadas pelo ar antes do revestimento. As grandes fábricas de fibra de telecomunicações possuem seções fechadas onde o gás é resfriado.
Algumas empresas também instalam torres de desenho em salas limpas. No entanto, a maioria dos fabricantes de fibras especiais utiliza ar ambiente limpo, com filtros HEPA instalados atrás das pré-formas e fornos, e em partes da torre.
6. Medição do diâmetro da fibra: O diâmetro das fibras especiais varia de 50 mícrons a 1.000 mícrons (1 mm). Os tamanhos amplamente utilizados incluem 80, 125 e 400 µm. O diâmetro é determinado pela velocidade de trefilação. Pequenas mudanças na temperatura do forno ou da pré-forma, no fluxo de gás inerte ou outras condições de estiragem podem causar pequenas flutuações no diâmetro da fibra.
Para evitar esta situação, a torre possui um sistema de medição contínua que envia dados para a malha de controle de diâmetro. A velocidade de tração do sem-fim pode ser ajustada usando esta informação. Em alguns casos, pode haver um circuito de controle secundário para ajustar a alimentação da pré-forma. Essas malhas de controle usam medições de diâmetro para fazer ajustes rápidos.
7. Sistema de revestimento: O revestimento de fibra é necessário para proteger as fibras de vidro e mantê-las fortes. Existem também algumas fibras especiais que necessitam de um revestimento para ajudar a melhorar o seu desempenho óptico. A maioria dos revestimentos tem duas camadas: uma camada interna mais macia e uma camada externa mais dura que fica presa ao vidro.
Isto significa que o sistema de revestimento deve aplicar e curar duas resinas separadas. A fibra entra no primeiro molde ou “copo” do sistema de revestimento, que aplica o revestimento primário (camada interna). Alguns revestimentos secundários, chamados de “umidificação em úmido”, podem ser aplicados antes da cura do revestimento primário.
8. Medição de concentricidade: O diâmetro da fibra e sua concentricidade devem ser medidos utilizando instrumentos baseados em laser. A força do material de revestimento ajuda a manter a fibra no meio do molde.
Se houver um problema com a concentricidade, o processo poderá precisar ser interrompido e reiniciado. É importante ter um revestimento correto na fibra para evitar microperdas por flexão, que podem causar problemas de atenuação.
9. Cabrestante e bobinas: O guincho na parte inferior da pré-forma puxa as fibras da sua extremidade. Existe também um sistema que enrola a fibra em uma bobina de armazenamento. A tensão na fibra é controlada para garantir que ela seja enrolada corretamente no eixo de enrolamento.
10. Testador de prova e rebobinador: A resistência à tração é uma medida fundamental para fibras acabadas. As fábricas usam essa medida para encontrar problemas com a pré-forma e o processo de elaboração. A máquina de inspeção possui um carretel de compensação, dois guinchos controláveis e um carretel de recolhimento.
O provador geralmente fica próximo ao guincho principal da torre de tração ou em uma sala separada. Alguns fabricantes de fibras especiais também possuem sistemas de rebobinagem para dividir a produção da pré-forma em vários rolos - no comprimento especificado pelo cliente da fibra.
11. Outros equipamentos de torre de tração: Alguns tipos de fibras necessitam de sistemas diferentes para controlar suas qualidades específicas. Por exemplo, fibras polarizadas circularmente e alguns outros tipos de fibras precisam ser girados ou torcidos durante o processo de trefilação.
Isto pode ser feito pelo girador no mandril de pré-forma ou pelo dispositivo de torção ou agitação abaixo. O desenho de fibras de cristal fotônico com espaços de ar, vazios e outros recursos pode exigir fluxo de gás adicional e sistemas de pressão de gás para controlar a pressão interna e a umidade.
2. Linha de produção com buffer apertado de controle HK-30 IPC + PLC
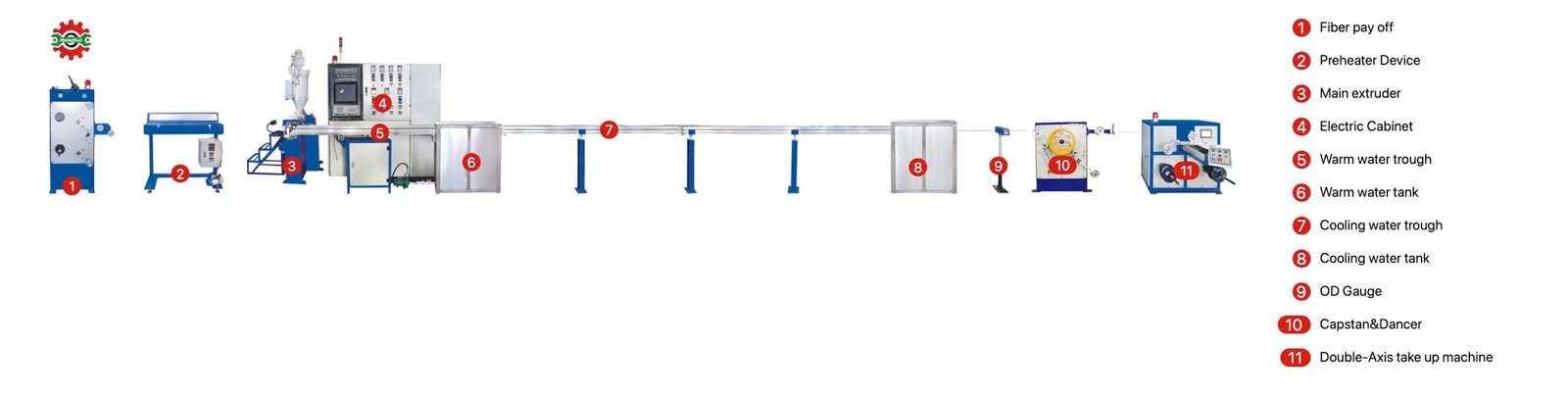
1. Fibra compensa: colocar 25km/50km fibra nua.
2. Dispositivo pré-aquecedor de fibra : aquecer a fibra antes da extrusora.
3. Extrusora principal: usando o parafuso da melhor qualidade da China, extrusão do PE/PVC/TPEE material; o motor usando Siemens mais um codificador e adota controle de circuito fechado para fazer com que a linha de produção para mudança de diâmetro seja mais estável durante o aumento ou diminuição da velocidade da linha.
4. Cabine de controle: Controle PLC+IPC, operação mais fácil para o trabalhador, o transdutor usando American Emerson/Mitsubishi, Japonês, outras peças elétricas usando Schneider.
5. Calha de água quente: usando água da torneira normal para resfriar o cabo
6. Tanque de água quente: Conecte a pia para reabastecer automaticamente a calha de água quente.
7. Calha de água de resfriamento: temperatura da água em torno de 10-25 graus Celsius para diâmetro externo estável de resfriamento.
8. Tanque de água de resfriamento: Ligação com a máquina Chiller, enchendo a água de resfriamento até a calha de água de resfriamento automática
9. Medidor de diâmetro externo: exibe o diâmetro real do cabo ao operador.
10. Cabrestante: alteração automática da velocidade da linha em Panasonic servo mais Caixa de velocidade.
11. Assumir: motor usando Siemens, atravessando por servo e também possui uma tela para aumentar/diminuir a velocidade do operador.
3. Controle HK-50 IPC+PLC Patch-Cord/Cabo Macio Linha de produção
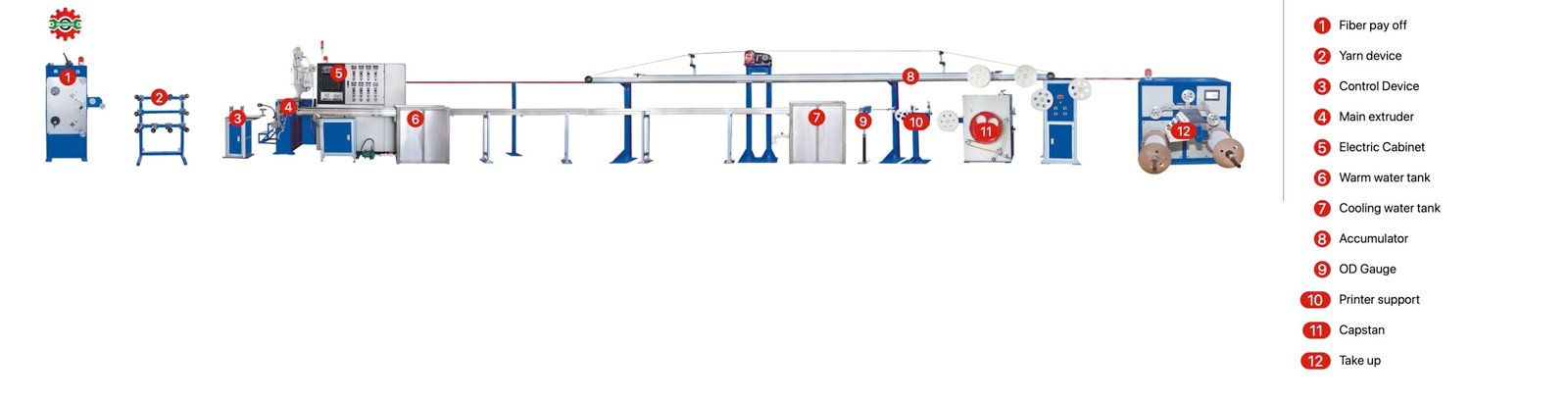
1. Fibra compensa: colocar 25km/50km fibra nua.
2. Dispositivo de fio: coloque o fio ao redor da fibra nua.
3. Plataforma de controle : controlar tudo (fibra, fio) antes da extrusora.
4. Extrusora principal: usando o parafuso da melhor qualidade da China, extrusão do LSZH/PVC material; o motor usando Siemens mais um codificador e adota controle de circuito fechado para fazer com que a linha de produção para mudança de diâmetro seja mais estável durante o aumento ou diminuição da velocidade da linha.
5. Cabine de controle: Controle PLC+IPC, operação mais fácil para o trabalhador, o transdutor usando American Emerson/Mitsubishi, Japonês, outras peças elétricas usando Schneider.
6. Tanque de água quente: Conecte a pia para reabastecer automaticamente a calha de água quente.
7. Tanque de água de resfriamento: Ligação com a máquina Chiller, enchendo a água de resfriamento até a calha de água de resfriamento automática
8. Medidor de diâmetro externo: exibe o diâmetro real do cabo ao operador.
9. Cabrestante: alteração automática da velocidade da linha em Panasonic servo mais Caixa de velocidade.
10. Eixo DuploAssumir: motor usando Siemens, atravessando por servo e também possui uma tela para aumentar/diminuir a velocidade do operador.
Abaixo está o link do vídeo de Linha de produção de patch cord/cabo flexível de controle IPC+PLC HK-50
Mundo final
se você está interessado neste projeto, vamos entre em contato com vocês para receber a oferta