ADSS cable production is a process that has traditionally been done by hand. However, with the advancement of technology, there are now machines that can produce ADSS cable quickly and easily. In this article, we will discuss the process of ADSS cable production and how to use machines to do it effectively.
1. Introduce the ADSS cable and its features
ADSS cable is a kind of optical fiber cable specially designed for aerial application. ADSS means All-Dielectric Self-Supporting. This type of cable usually has a core made of dielectric material and a sheath made of plastic or metal, which makes it has good characteristics of dielectric and corrosion resistance.
ADSS is usually used for long-distance and metropolitan area network applications where underground cables are not suitable due to environmental restrictions such as terrain or urban congestion.
The advantages of ADSS over traditional ADSS cables include its small size, lightweight, and low installation costs. ADSS also has good mechanical and environmental properties, making it an ideal choice for aerial applications. Thanks to these features, ADSS has become one of the most popular types of optical fiber cables in the world.
2. Describe the production process of the ADSS cable
According to the picture it is easy to see what the structure of ADSS cable is composed of:
- Colored fiber
- fiber jelly
- loose tube
- FRP
- Water blocking tape
- Aramid Yarns
- Water blocking Yarn
- Rip cord
- HDPE Sheath
Now let’s see how to produce ADSS cable by machines:
To create ADSS cable, the first step is to color the Bard fiber in 12 different colors. This can be done easily by using machines:
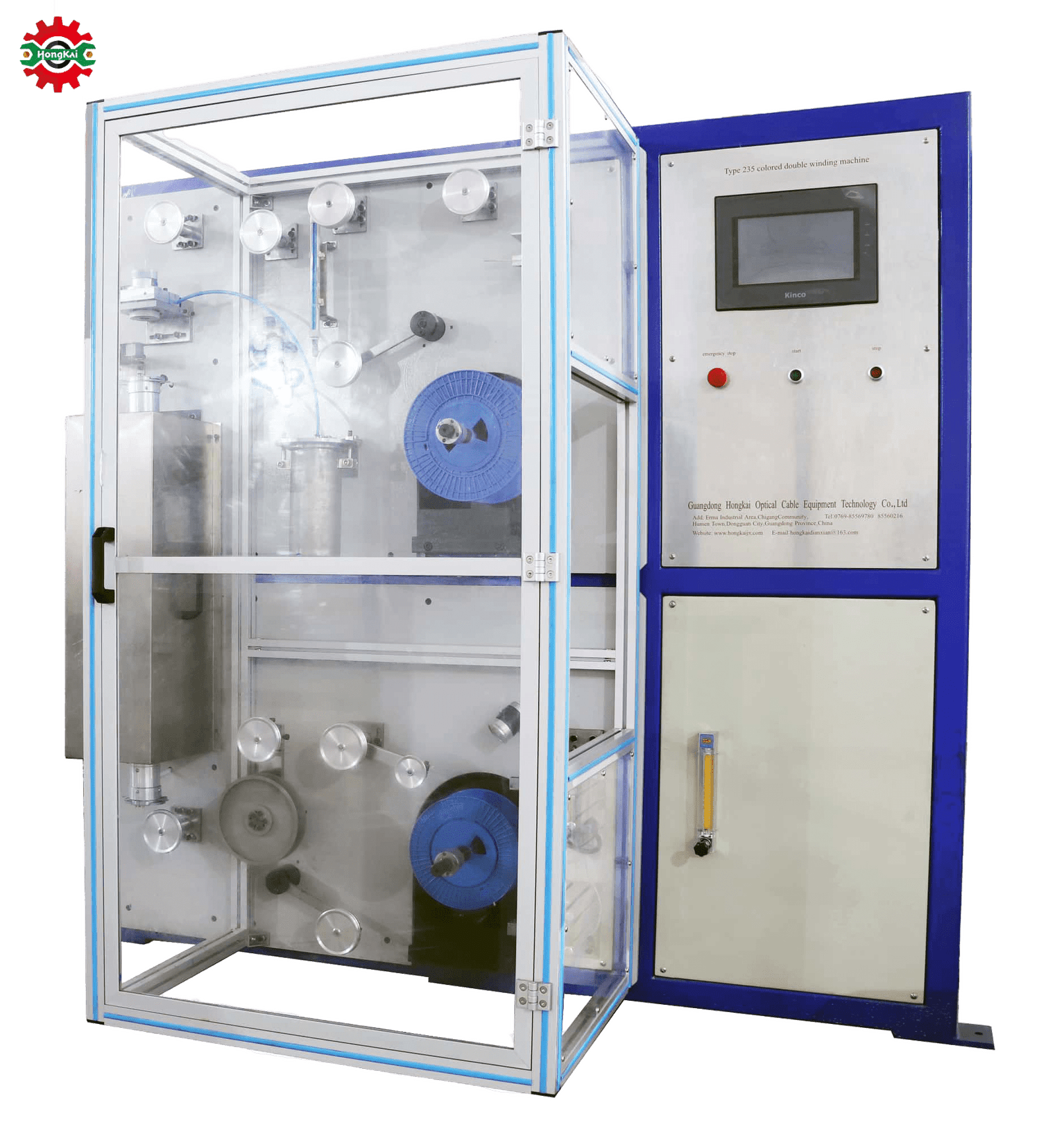
The second step in the ADSS cable production process is to apply fiber jelly to the colored fibers inside the loose tube. This protects the fibers from damage and ensures that they will remain intact during the manufacturing process.
so the loose tube production line is the first step to making the ADSS cable:

The third step is to strand the 6-12 loose tubes around the FRP, then binding them by the water blocking yarn and the water blocking tape cover later.

The final step in the ADSS cable production process is to apply a rip cord and aramid yarns. This helps to protect the fibers from damage and ensures that the cable will be able to withstand harsh environmental conditions. The rip cord at the end of the cable makes it easy to tear through the sheath when it needs to be installed.

3. Show how our machines make the production process more efficient and easier to control
a. HK-235 Coloring And Rewinding Machine
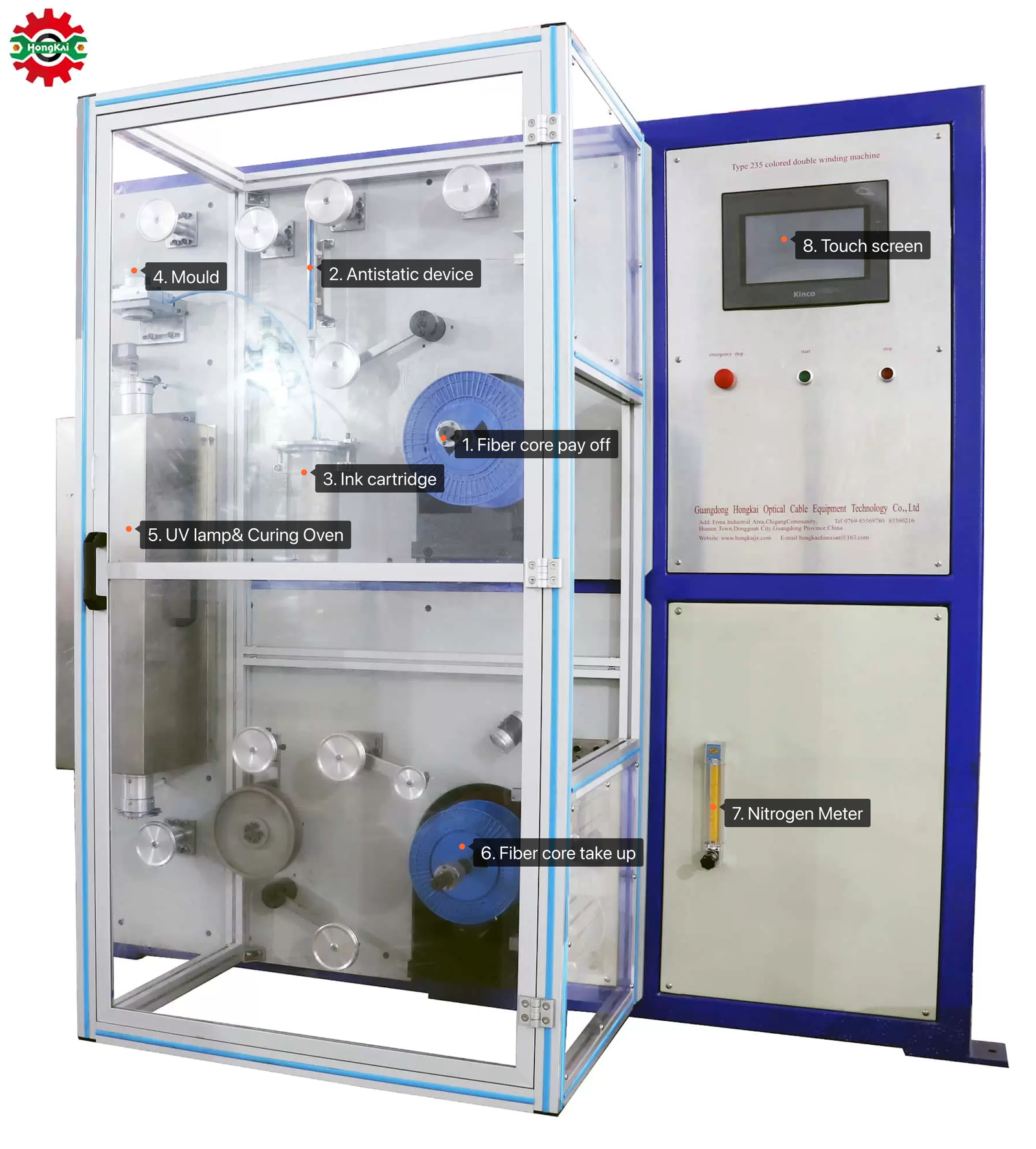
1. Fiber core pay off: put on 25km/50km bare fiber.
2. Antistatic Device: Remove debris from the fiber surface due to the high-speed process in the air.
3. Ink cartridge: Used to store the colors to be colored.
4. Mould: Make sure the diameter of the fiber core is the same.
5. UV lamp& Curing oven: The German power supply stabilizes the output voltage to the UV lamp to ensure a stable temperature, and then the curing oven allows the color to adhere to the surface of the bare fiber.
6. Fiber core take up: Fully automatic sweeping tray and also an additional de-static device.
7.Nitrogen meter: Nitrogen can increase the adhesion of the ink, you can use this table to adjust the input size of nitrogen.
8. Touch screen: Human-machine interface for automated operation.
b. HK-50 IPC+PLC Control Loose Tube Production Line

1. Fibber pay off: put on 1-12 Dish of the 25km/50km bare fiber, And for the convenience of our customers, we have marked the position of each color placement.
2. Jelly Machine: Fully automatic jelly filling/circulation system to achieve bubble-free and stable filling.
3. Extruder: Support PBT/PP material, and stable glue output to ensure stable outside diameter during acceleration and deceleration.
4. Cabinet: The use of the front and weak power separated electrical cabinet, Siemens PLC, and visualization of the operating system so that the operator faster and more stable production of qualified products.
5. Warm water tank: A cooling system with internal circulation is used to lower the surface of the cable by water cooling in order to achieve a stable outside diameter.
6. Capstan: Fully automatic sweeping tray and also an additional de-static device.
7. Nitrogen meter: Nitrogen can increase the adhesion of the ink, you can use this table to adjust the input size of nitrogen.
8. Touch screen: Human-machine interface for automated operation.
C. HK-800/12 SZ Stranding Production Line

1. Member pay off: For placing central reinforcements, such as FRP or steel wire which between the loose tubes.
2. 12 sets tube pay off: Up to 1-12 loose tubes can be placed.
3. Jelly device: Can be used to fill the jelly paste in the process of stranding to avoid the friction generated in the middle of the process of stranding.
3. SZ stranding device: S/Z stranding allows 12 tubes to be stranded at the same pitch while maintaining the same tension on each one.
4. Binding Yarn: The reason for using double-head yarn tying here is to prevent the loose tube after stranding, and the most important issue in this step is to maintain pressure on each bundle during the tying process.
5. water-blocking : double head water blocking tape, This compound helps to create a barrier between the cable and the water, preventing any damage from occurring. Water blocking tape is often used in applications where moisture is present, such as in exposed outdoor wiring.
6. Binding Yarn: single head binding yarn device, What it does is once again put all the ties together.
7. Capstan: 800mm double wheel capstan, Can adjust tension by air pressure when production, can feedback the signal to take up to track the line speed when movable wheel move.
8. Dancer : Cylinder dancer for better tension control, giving start and stop signals to the winder.
9. Take up: 800-1600mm Gantry type, automatic traverse, Siemens PLC control and touch screen.
D. HK-90 IPC+PLC Control Cable Sheathing Production Line

1. 800-1600mm Gantry type pay off: Motor: Siemens, Drive: Emerson, Touch screen: Siemens, PLC system: Siemens s7-1200
2. Cylinder dancer: linkage with the pay off, Potentiometer + cylinder control
3. Aramid yarn stranding device* 2: 24-heads magnetic damping control
4. Jelly filling machine: Filled with oil around the cable to achieve protection.
5. Armored device:
a. Double heads steel aluminum tape pay off: put on steel-aluminum.
b. On-line seam welding device: joint weld steel& Aluminum tape when changing one tape drum to another.
c.Metal tape corrugating device: corrugated the steel aluminum before extruder.
d.Metal tape longitudinal forming device: longitudinal forming and fixed diameter before the extruder
6. Main extruder: using the best quality screw from China, extrusion the PE/PVC material. and the motor using Siemens.
7. Control cabinet: PLC+IPC control, more easy operation for the worker, the transducer using American Emerson, other electric parts using Schneider.
8. Warm and Cooling Water Trough: cooling the wire down slowly.
9. Diameter Gauge: display the actual diameter of the cable to the operator.
10. Capstan:Power: 7.5KW Siemens motor + Deceleration Box + 7.5KW American Emerson transducer + speed-governor.
11. Power frequency spark machine: Online test for outer sheathing breakage.
12. Printer machine: Using thermal printing + embossing method to print the required font on the cable surface
13. Cylinder dancer: linkage with the take up, Potentiometer + cylinder control
14. 800-1600mm Gantry type take up: Motor: Siemens, Drive: Emerson, Touch screen: Siemens, PLC system: Siemens s7-1200
4. Discuss the benefits of using machines in the production of ADSS cables
Machines play an important role in the production of ADSS cables. The benefits of using machines include: increased speed and efficiency, reduced costs, improved safety, and consistent quality.
Machines can work faster and more accurately than humans, meaning that more cables can be produced in a shorter time frame. This leads to reduced costs as well as increased productivity. In addition, machines are not susceptible to human error, which can often lead to costly mistakes.
Finally, machines produce cables with a consistent level of quality, ensuring that each cable meets strict standards. When used in conjunction with skilled workers, machines a can produce high-quality ADSS cables quickly and efficiently.
5. Conclusion paragraph
That’s it! We have covered the steps involved in producing ADS cables by machines. If you have any questions or need more information, please don’t hesitate to contact us. We would be happy to help you get your project off the ground. Thanks for reading!