Apa itu Kabel Drop FTTH?
Dari struktur di bawah ini, terlihat secara visual bahwa strukturnya terdiri dari bagian-bagian berikut:
- Serat
- FRP/Kawat baja
- Anggota (tali kawat baja)
- selubung LSZH
Jadi jika kita analisa berdasarkan tulisan kami sebelumnya: Cara Memilih Lini Produksi Sesuai dengan Kabel Optik yang Berbeda, Hal ini dilakukan oleh mesin berikut:
- Menara Gambar
- HK-50 IPC+PLC Kontrol lini produksi kabel drop FTTH
Bagaimana cara membuat kabel drop FTTH dengan mesin?
Menara Gambar
Inti dan lapisan serat optik terbuat dari kaca silika yang sangat murni. Serat optik terbuat dari silika dengan salah satu dari dua cara. Metode yang pertama adalah metode wadah. Dalam metode ini, bubuk silikon dilebur untuk menghasilkan serat multimode yang lebih gemuk, yang cocok untuk transmisi jarak pendek banyak sinyal gelombang cahaya. Metode kedua, deposisi uap, menghasilkan silinder padat yang terdiri dari bahan inti dan bahan pelapis, yang kemudian dipanaskan dan ditarik ke dalam serat optik mode tunggal yang lebih tipis untuk komunikasi jarak jauh.
Spesifikasi Menara Gambar
- Modul umpan awal
- Perapian
- Perakitan traktor permulaan
- Sistem pasokan gas (untuk argon)
- Filter HEPA
- Pengukuran diameter serat
- Sistem pelapisan serat
- Oven pengawetan UV dan termal
- Pengukuran diameter lapisan
- Kontrol pemusatan serat
- Kontrol konsentrisitas lapisan serat
- Pengukuran ketegangan serat
- Penggulung / penarik fiber
- Penggulung serat/pengubah drum
- Penguji/rewinder tahan serat
1. Modul umpan preform: Bentuk awal dimasukkan ke dalam tungku. Kecepatan dan penempatan preform dikontrol sehingga berada di tengah tungku. Kecepatan turunnya preform ke dalam tungku ditentukan oleh seberapa cepat kawat ditarik, ukuran preform, dan seberapa tipis serat yang Anda inginkan.
Diameter serat disesuaikan dengan seberapa cepat kawat ditarik. Ketegangan regangan dikendalikan oleh seberapa panas tungku. Ketegangan ini perlu dipantau dan dijaga konstan selama penarikan sehingga serat tidak ditarik terlalu kencang atau terlalu longgar.
2. Perapian: Bentuk awal dimasukkan ke dalam lubang di bagian atas tungku. Tungku berbentuk silinder dan memiliki sumbu vertikal. Ada lubang di permukaan bawah tempat keluarnya serat berdiameter kecil. Kedua lubang memiliki iris untuk mengubah diameternya, sehingga memungkinkan operator mengontrol aliran gas di dalam tungku.
Tungku menggunakan elemen listrik bertegangan tinggi-biasanya unit resistansi grafit. Untuk memulai menggambar kawat, bentuk awal dimasukkan ke dalam tungku. Zona gambar dipanaskan hingga di atas 1900°C, saat kaca melunak dan meregang, dan tetesan air menarik serat ke bawah.
3. Perakitan traktor permulaan: Air yang menetes di bawah tungku dipotong. Serat tersebut kemudian melewati traktor roda dua yang menariknya ke bawah. Diameter serat diperkecil hingga mencapai spesifikasi yang benar.
Kemudian serat masuk ke sistem pelapisan dan mengikuti menara ke bawah. Di sana, sebuah winch mengambil alih dan menarik mereka ke bawah. Setelah itu, winch di bagian bawah mengontrol seberapa cepat serat disusun berdasarkan putaran umpan balik dengan pengukur diameter.
4. Pasokan gas untuk tungku: Tungkunya sangat panas, sekitar 2000°C. Namun jika suhu menjadi terlalu tinggi, lebih dari 600 hingga 800°C, grafit akan mulai terurai dan menimbulkan polusi.
Untuk menghindari hal ini, argon digunakan untuk membantu mengontrol suhu. Argon juga membantu menghentikan turbulensi di udara yang dapat menimbulkan kerusakan. Saat argon mengalir melalui tungku, kami menggunakan iris untuk mengontrol berapa banyak argon yang masuk dan keluar. Penting untuk menjaga aliran argon tetap tepat, jadi kami menggunakan teknik berbeda untuk melakukannya.
5. Penyaringan udara: Kecepatan penyusunan lambat yang digunakan untuk serat khusus berarti bahwa serat yang tidak dilapisi biasanya didinginkan oleh udara sebelum dilapisi. Pabrik serat telekomunikasi yang lebih besar memiliki bagian tertutup tempat gas didinginkan.
Beberapa perusahaan juga mendirikan menara perancangan di ruangan yang bersih. Namun, sebagian besar produsen serat khusus menggunakan udara sekitar yang bersih – dibersihkan dengan filter HEPA yang dipasang di belakang preform dan tungku, dan di beberapa bagian menara.
6. Pengukuran diameter serat: Diameter serat khusus berkisar antara 50 mikron hingga 1.000 mikron (1 mm). Ukuran yang banyak digunakan meliputi 80, 125 dan 400 µm. Diameternya ditentukan oleh kecepatan menggambar. Perubahan kecil pada suhu tungku atau suhu awal, aliran gas inert, atau kondisi penarikan lainnya dapat menyebabkan fluktuasi kecil pada diameter serat.
Untuk menghindari situasi ini, menara memiliki sistem pengukuran terus menerus yang mengirimkan data ke loop kendali diameter. Kecepatan traksi auger dapat diatur menggunakan informasi ini. Dalam beberapa kasus, mungkin terdapat loop kontrol sekunder untuk menyesuaikan umpan yang telah dibentuk sebelumnya. Loop kontrol ini menggunakan pengukuran diameter untuk melakukan penyesuaian cepat.
7. Sistem pelapisan: Lapisan serat diperlukan untuk melindungi serat kaca dan menjaganya tetap kuat. Ada juga beberapa serat khusus yang memerlukan lapisan untuk membantu meningkatkan kinerja optiknya. Kebanyakan pelapis memiliki dua lapisan: lapisan dalam yang lebih lembut dan lapisan luar yang lebih keras yang menempel pada kaca.
Ini berarti sistem pelapisan harus menerapkan dan menyembuhkan dua resin terpisah. Serat memasuki cetakan atau “cangkir” pertama dari sistem pelapisan, yang menerapkan pelapisan primer (lapisan dalam). Beberapa pelapis sekunder, yang disebut “pelembapan saat basah”, dapat diaplikasikan sebelum lapisan primer diawetkan.
8. Pengukuran konsentrisitas: Diameter serat dan konsentrisitasnya harus diukur menggunakan instrumen berbasis laser. Kekuatan bahan pelapis membantu menjaga serat tetap berada di tengah cetakan.
Jika ada masalah dengan konsentrisitas, maka proses tersebut mungkin perlu dihentikan dan dimulai kembali. Penting untuk memiliki lapisan yang benar pada serat untuk menghindari kerugian mikro lentur, yang dapat menyebabkan masalah atenuasi.
9. Penggulung dan ambil gulungan: Winch di bagian bawah preform menarik serat dari ujungnya. Ada juga sistem yang menggulung serat ke gulungan penyimpanan. Ketegangan pada serat dikontrol untuk memastikan serat digulung dengan benar pada poros pengambil.
10. Penguji bukti dan penggulung ulang: Kekuatan tarik adalah ukuran utama serat jadi. Pabrik menggunakan pengukuran ini untuk menemukan masalah pada proses preform dan drafting. Mesin inspeksi memiliki gulungan pembayaran, dua derek yang dapat dikontrol, dan gulungan pengambil.
Proofer biasanya berada di dekat winch utama menara traksi atau di ruangan terpisah. Beberapa produsen serat khusus juga memiliki sistem penggulungan ulang untuk membagi keluaran bentuk awal menjadi beberapa gulungan-untuk panjang yang ditentukan oleh pelanggan serat.
11. Peralatan menara undian lainnya: Beberapa jenis serat memerlukan sistem berbeda untuk mengontrol kualitas spesifiknya. Misalnya, serat terpolarisasi sirkular dan beberapa jenis serat lainnya perlu diputar atau dipelintir selama proses menggambar.
Hal ini dapat dilakukan dengan pemintal di dalam chuck yang telah dibentuk sebelumnya atau dengan alat pemutar atau pengocok di bawahnya. Menggambar serat kristal fotonik dengan celah udara, rongga, dan fitur lainnya mungkin memerlukan sistem aliran gas dan tekanan gas tambahan untuk mengontrol tekanan dan kelembapan internal.
Kontrol IPC+PLC HK-50 Kabel Jatuhkan FTTH Garis produksi
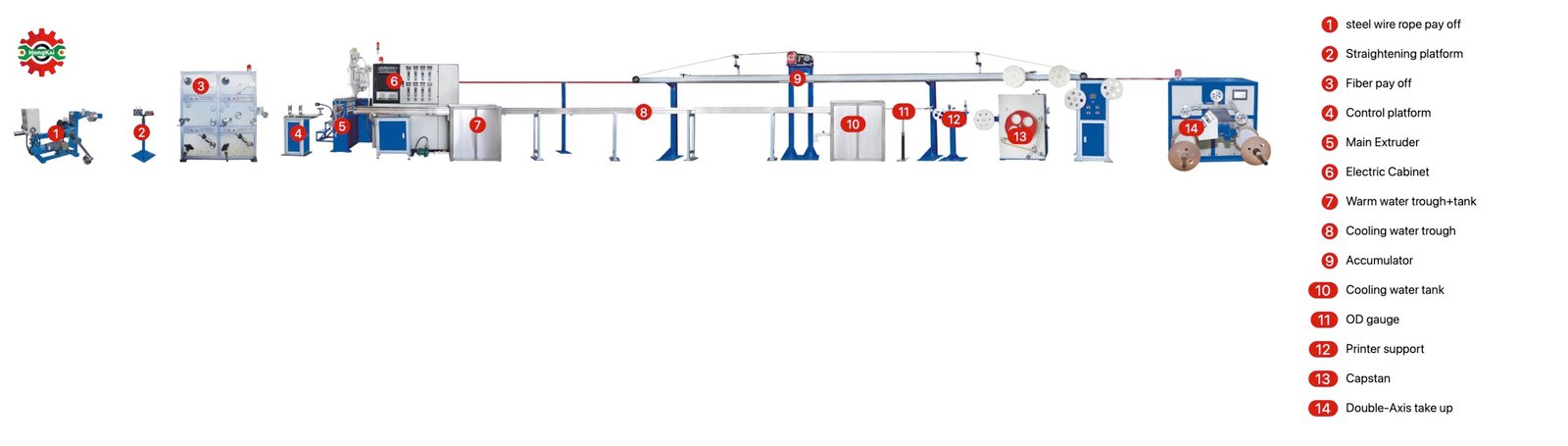
- Tali kawat baja membuahkan hasil: kenakan tali kawat baja 1,0-1,2 mm sebagai Anggota (tali kawat baja) yang disebutkan dalam struktur.
- Platform Pelurusan: Luruskan kawat sebelum masuk ke kepala silang
- Serat membayar: pakai 25km/50km serat telanjang.
- Platform Kontrol : mengontrol semuanya (serat, kawat baja & tali kawat baja) sebelum ekstruder.
- ekstruder utama: menggunakan sekrup kualitas terbaik dari China, ekstrusi LSZH/PVC bahan; motor yang digunakan Siemens ditambah sebuah pembuat enkode dan mengadopsi kontrol loop tertutup untuk membuat jalur produksi untuk perubahan diameter lebih stabil selama kecepatan jalur bertambah atau berkurang.
- Kabinet kontrol: Kontrol PLC+IPC, pengoperasian lebih mudah bagi pekerja, transduser menggunakan Amerika Emerson/Mitsubishi, Jepang, penggunaan suku cadang listrik lainnya Schneider.
- Tangki air hangat: Hubungkan wastafel untuk mengisi kembali bak air hangat secara otomatis.
- Palung air pendingin: suhu air sekitar 10-25 derajat celsius untuk mendinginkan diameter luar yang stabil.
- Tangki air pendingin: Keterhubungan dengan mesin Chiller, pengisian air pendingin ke bak air pendingin otomatis
- Pengukur OD: menampilkan diameter kabel sebenarnya kepada operator.
- Putaran jangkar: otomatis mengubah kecepatan saluran sebesar panasonic servo ditambah kotak roda gigi.
- Sumbu GandaMengambil: penggunaan motor Siemens, melintasi servo dan di sana juga terdapat tampilan layar untuk menaikkan/menurunkan kecepatan operator.
Dibawah ini link videonya HK-50 IPC+PLC Kontrol lini produksi kabel drop FTTH
Dunia terakhir
jika Anda tertarik dengan proyek ini, ayo hubungi kamus untuk mendapatkan tawaran itu