Cáp đệm chặt là gì?
Đối với cấu trúc bên trái, Cấu trúc đệm chặt sử dụng sợi đệm 900μm. Lõi được bảo vệ bởi một lớp phủ. Vật liệu phủ là PE/PVC/TPEE
Vì vậy, Cáp đệm chặt cần hai bước để tạo ra nó từ phân tích cấu trúc:
- Tháp vẽ
- Dây chuyền sản xuất đệm chặt điều khiển HK-30 IPC+PLC
Làm thế nào để làm cho đệm chặt bằng máy?
1. Tháp vẽ
Lõi và vỏ bọc của sợi quang được làm bằng thủy tinh silica có độ tinh khiết cao. Sợi quang được làm từ silica theo một trong hai cách. Phương pháp đầu tiên là phương pháp nồi nấu kim loại. Trong phương pháp này, bột silicon được nấu chảy để tạo ra sợi đa mode béo hơn, phù hợp cho việc truyền dẫn nhiều tín hiệu sóng ánh sáng ở khoảng cách ngắn. Phương pháp thứ hai, lắng đọng hơi, tạo ra một hình trụ rắn bao gồm vật liệu lõi và vật liệu bọc, sau đó được nung nóng và kéo thành sợi quang đơn mode mỏng hơn để liên lạc ở khoảng cách xa.
Đặc điểm kỹ thuật của Tháp vẽ
- Mô-đun cấp phôi
- Lò lửa
- Cụm máy kéo khởi động
- Hệ thống cấp khí (cho argon)
- bộ lọc HEPA
- Đo đường kính sợi
- Hệ thống phủ sợi
- Lò sấy UV và nhiệt
- Đo đường kính lớp phủ
- Kiểm soát định tâm sợi
- Kiểm soát độ đồng tâm lớp phủ sợi
- Đo độ căng sợi
- Capstan / bộ kéo sợi
- Máy cuộn sợi/bộ thay trống
- Máy kiểm tra / cuộn lại sợi
1. Mô-đun nguồn cấp dữ liệu phôi: Các khuôn phôi được đưa vào lò nung. Tốc độ và vị trí của phôi được kiểm soát sao cho chúng ở giữa lò. Tốc độ mà các khuôn phôi đi xuống lò được thiết lập bởi tốc độ rút dây, kích thước của khuôn phôi và độ mỏng mà bạn muốn sợi.
Đường kính sợi được điều chỉnh bằng tốc độ rút dây. Độ căng kéo dài được kiểm soát bởi độ nóng của lò. Độ căng này cần được theo dõi và giữ không đổi trong quá trình kéo để sợi không bị kéo quá chặt hoặc quá lỏng.
2. Lò lửa: Phôi được đưa vào lỗ trên đỉnh lò. Lò có dạng hình trụ và có trục thẳng đứng. Có một lỗ ở bề mặt phía dưới để từ đó các sợi có đường kính nhỏ thoát ra. Cả hai lỗ đều có tròng để thay đổi đường kính, cho phép người vận hành kiểm soát được dòng khí trong lò.
Lò sử dụng một bộ phận điện cao áp - thường là bộ phận điện trở than chì. Để bắt đầu kéo dây, phôi được đưa vào lò nung. Vùng vẽ được làm nóng đến trên 1900°C, nơi kính mềm ra và giãn ra, còn các giọt nước sẽ kéo các sợi vải xuống.
3. Cụm máy kéo khởi động: Nước nhỏ giọt phía dưới lò bị cắt. Sợi sau đó đi qua một máy kéo hai bánh để kéo nó xuống. Đường kính của sợi được giảm cho đến khi đạt được thông số kỹ thuật chính xác.
Sau đó, các sợi đi vào hệ thống phủ và theo tháp xuống phía dưới. Ở đó, một tời sẽ tiếp quản và kéo chúng xuống. Sau đó, tời ở phía dưới sẽ kiểm soát tốc độ kéo sợi dựa trên vòng phản hồi bằng máy đo đường kính.
4. Cung cấp khí cho lò: Lò rất nóng, khoảng 2000°C. Nhưng nếu nhiệt độ quá cao, trên 600 đến 800°C, than chì sẽ bắt đầu phân hủy và gây ô nhiễm.
Để tránh điều này, argon được sử dụng để giúp kiểm soát nhiệt độ. Argon cũng giúp ngăn chặn sự nhiễu loạn trong không khí có thể gây hư hỏng. Khi argon chảy qua lò, chúng tôi sử dụng mống mắt để kiểm soát lượng khí vào và ra. Điều quan trọng là phải duy trì dòng khí argon chính xác, vì vậy chúng tôi sử dụng các kỹ thuật khác nhau để thực hiện điều đó.
5. Lọc không khí: Tốc độ kéo dài chậm được sử dụng cho các loại xơ đặc biệt có nghĩa là xơ không tráng phủ thường được làm mát bằng không khí trước khi phủ. Các nhà máy cáp quang viễn thông lớn hơn có các khu vực khép kín nơi khí được làm mát.
Một số công ty còn lắp đặt tháp soạn thảo trong phòng sạch. Tuy nhiên, hầu hết các nhà sản xuất sợi đặc biệt đều sử dụng không khí sạch xung quanh – được làm sạch bằng bộ lọc HEPA được lắp đặt phía sau khuôn phôi và lò nung cũng như trong các bộ phận của tháp.
6. Đo đường kính sợi: Đường kính của sợi đặc biệt dao động từ 50 micron đến 1.000 micron (1 mm). Các kích thước được sử dụng rộng rãi bao gồm 80, 125 và 400 µm. Đường kính được xác định bởi tốc độ vẽ. Những thay đổi nhỏ về nhiệt độ lò hoặc phôi, dòng khí trơ hoặc các điều kiện kéo dài khác có thể gây ra những biến động nhỏ về đường kính sợi.
Để tránh tình trạng này, tháp có hệ thống đo liên tục gửi dữ liệu đến vòng kiểm soát đường kính. Tốc độ kéo của máy khoan có thể được điều chỉnh bằng thông tin này. Trong một số trường hợp, có thể có một vòng điều khiển thứ cấp để điều chỉnh nguồn cấp phôi. Các vòng điều khiển này sử dụng phép đo đường kính để điều chỉnh nhanh chóng.
7. Hệ thống phủ: Lớp phủ sợi là cần thiết để bảo vệ sợi thủy tinh và giữ cho chúng chắc chắn. Ngoài ra còn có một số loại sợi đặc biệt cần lớp phủ để giúp cải thiện hiệu suất quang học của chúng. Hầu hết các lớp phủ đều có hai lớp: lớp bên trong mềm hơn và lớp bên ngoài cứng hơn được gắn vào kính.
Điều này có nghĩa là hệ thống phủ phải áp dụng và xử lý hai loại nhựa riêng biệt. Sợi đi vào khuôn đầu tiên hoặc “cốc” của hệ thống phủ, áp dụng lớp phủ chính (lớp bên trong). Một số lớp phủ thứ cấp, được gọi là “làm ẩm khi ướt”, có thể được áp dụng trước khi lớp phủ chính được xử lý.
8. Đo độ đồng tâm: Đường kính của sợi và độ đồng tâm của nó phải được đo bằng các dụng cụ dựa trên tia laser. Lực của vật liệu phủ giúp giữ sợi ở giữa khuôn.
Nếu có vấn đề về độ đồng tâm thì quá trình này có thể cần phải dừng lại và bắt đầu lại. Điều quan trọng là phải có lớp phủ phù hợp trên sợi quang để tránh tổn thất do uốn vi mô, có thể gây ra các vấn đề suy giảm.
9. Capstan và bắt cuộn phim: Tời ở dưới cùng của phôi kéo các sợi từ phần cuối của phôi. Ngoài ra còn có một hệ thống cuộn sợi vào cuộn lưu trữ. Độ căng trên sợi được kiểm soát để đảm bảo nó được quấn chính xác vào trục cuốn.
10. Máy kiểm tra và tua lại bằng chứng: Độ bền kéo là thước đo quan trọng đối với sợi thành phẩm. Các nhà máy sử dụng phép đo này để tìm ra các vấn đề với quá trình tạo phôi và kéo dài. Máy kiểm tra có một cuộn thu hồi, hai tời điều khiển và một cuộn thu hồi.
Máy thử thường ở gần tời chính của tháp kéo hoặc trong một phòng riêng. Một số nhà sản xuất sợi đặc biệt cũng có hệ thống quấn lại để chia đầu ra của phôi thành nhiều cuộn - theo chiều dài do khách hàng sợi chỉ định.
11. Thiết bị tháp vẽ khác: Một số loại sợi cần các hệ thống khác nhau để kiểm soát chất lượng cụ thể của chúng. Ví dụ, sợi phân cực tròn và một số loại sợi khác cần được quay hoặc xoắn trong quá trình kéo.
Điều này có thể được thực hiện bằng máy quay trong mâm cặp tạo phôi hoặc thiết bị xoắn hoặc lắc bên dưới. Việc vẽ các sợi tinh thể quang tử có khe hở không khí, khoảng trống và các tính năng khác có thể yêu cầu hệ thống lưu lượng khí và áp suất khí bổ sung để kiểm soát áp suất và độ ẩm bên trong.
2. Dây chuyền sản xuất đệm chặt chẽ của HK-30 IPC+PLC
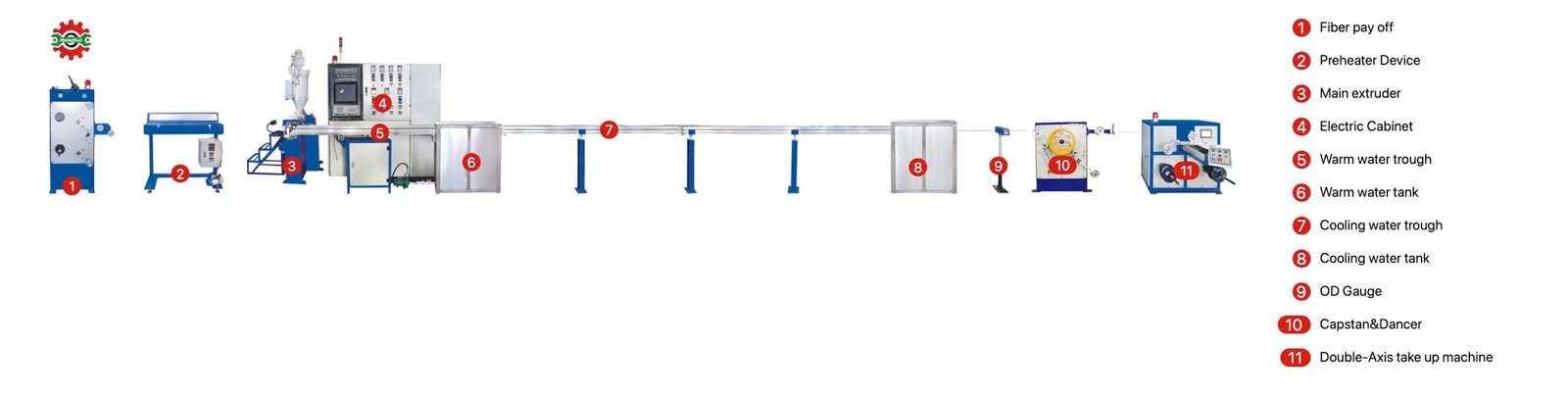
1. Chất xơ trả hết: mặc 25km/50km sợi trần.
2. Thiết bị làm nóng sợi quang : làm nóng sợi trước khi ép đùn.
3. Máy đùn chính: sử dụng vít chất lượng tốt nhất từ Trung Quốc, ép đùn PE/PVC/TPEE vật liệu; động cơ sử dụng Siemens cộng với một mã hoá và áp dụng điều khiển vòng kín để làm cho dây chuyền sản xuất thay đổi đường kính ổn định hơn trong quá trình tăng hoặc giảm tốc độ dây chuyền.
4. Tủ điều khiển: Điều khiển PLC+IPC, vận hành dễ dàng hơn cho công nhân, đầu dò sử dụng công nghệ Mỹ Emerson/Mitsubishi, Nhật Bản, các bộ phận điện khác sử dụng Schneider.
5. Máng nước ấm: sử dụng nước máy thông thường để làm mát cáp
6. Bình nước ấm: Kết nối bồn rửa để tự động bổ sung máng nước ấm.
7. Máng nước làm mát: nhiệt độ nước khoảng 10-25 độ C để làm mát đường kính ngoài ổn định.
8. Bể chứa nước làm mát: Liên kết với máy Chiller, nạp nước làm mát vào máng nước làm mát tự động
9. Máy đo OD: hiển thị đường kính thực tế của cáp cho người vận hành.
10. thuyền trưởng: tự động thay đổi tốc độ đường truyền bằng cách Panasonic servo cộng với Hộp số.
11.Nhặt lên: sử dụng động cơ Siemens, đi ngang qua phụ trợ và còn có màn hình hiển thị để người vận hành tăng/giảm tốc độ.
Thế giới cuối cùng
nếu bạn quan tâm đến dự án này, hãy liên hệ với bạns để nhận được ưu đãi