کابل بافر محکم چیست؟
از ساختار سمت چپ، ساختار Tight-buffered از فیبرهای بافر شده 900 میکرومتری استفاده میکند. هسته توسط یک پوشش لایهای محافظت میشود. جنس پوشش PE/PVC/TPEE است.
بنابراین کابل Tight-Buffered برای تولید از تحلیل ساختاری به دو مرحله نیاز دارد:
- برج طراحی
- خط تولید بافر محکم کنترلی HK-30 IPC+PLC
چگونه میتوان بافر محکمی توسط ماشینها ایجاد کرد؟
۱. برج نقشهکشی
هسته و روکش فیبر نوری از شیشه سیلیس با خلوص بالا ساخته شدهاند. فیبرهای نوری از سیلیس به یکی از دو روش زیر ساخته میشوند. روش اول، روش بوتهای است. در این روش، پودر سیلیکون ذوب میشود تا یک فیبر چند حالته ضخیمتر تولید شود که برای انتقال سیگنالهای موج نور در فواصل کوتاه مناسب است. روش دوم، رسوب بخار، یک استوانه جامد متشکل از یک ماده هسته و یک ماده روکش تولید میکند که سپس گرم شده و به یک فیبر نوری تک حالته نازکتر برای ارتباطات از راه دور تبدیل میشود.
مشخصات برج طراحی
- ماژول تغذیه پیش فرم
- کوره
- مونتاژ تراکتور راه اندازی
- سیستم تامین گاز (برای آرگون)
- فیلترهای هپا
- اندازهگیری قطر الیاف
- سیستم پوشش الیاف
- کورههای پخت UV و حرارتی
- اندازهگیری قطر پوشش
- کنترل مرکزیت فیبر
- کنترل غلظت پوشش الیاف
- اندازهگیری کشش الیاف
- چرخ تسمه / کشنده الیاف
- دستگاه پیچنده/تعویض درام الیاف
- تستر/روپیچنده فیبر نوری
1. ماژول تغذیه پیش فرم: پیشفرمها در کوره قرار میگیرند. سرعت و نحوه قرارگیری پیشفرمها طوری کنترل میشود که در وسط کوره قرار گیرند. سرعت پایین رفتن پیشفرمها به داخل کوره با سرعت کشش سیم، اندازه پیشفرم و میزان نازکی الیاف مورد نظر شما تنظیم میشود.
قطر الیاف با سرعت کشش سیم تنظیم میشود. کشش کششی با میزان گرمای کوره کنترل میشود. این کشش باید در طول کشش کنترل و ثابت نگه داشته شود تا الیاف خیلی سفت یا خیلی شل کشیده نشوند.
2. کورهپیشسازه در سوراخی در بالای کوره قرار میگیرد. کوره استوانهای شکل است و دارای محور عمودی میباشد. سوراخی در سطح زیرین وجود دارد که الیاف با قطر کوچک از آن خارج میشوند. هر دو سوراخ دارای دیافراگمهایی برای تغییر قطر هستند که به اپراتور اجازه میدهد جریان گاز در کوره را کنترل کند.
کوره از یک المان الکتریکی ولتاژ بالا - معمولاً یک واحد مقاومت گرافیتی - استفاده میکند. برای شروع کشش سیم، پیشسازه در کوره قرار میگیرد. ناحیه کشش تا دمای بالای ۱۹۰۰ درجه سانتیگراد گرم میشود، جایی که شیشه نرم و کشیده میشود و قطرات آب الیاف را به پایین میکشند.
3. مونتاژ تراکتور راه اندازی: آبی که از زیر کوره میچکد، بریده میشود. سپس الیاف از طریق یک تراکتور دو چرخ که آن را به پایین میکشد، عبور میکند. قطر الیاف کاهش مییابد تا به مشخصات صحیح برسد.
سپس الیاف وارد یک سیستم پوششدهی میشوند و از طریق یک برج به پایین میروند. در آنجا، یک وینچ آنها را به پایین میکشد. پس از آن، وینچ در پایین، سرعت کشیده شدن الیاف را بر اساس یک حلقه بازخورد با قطرسنج کنترل میکند.
4. تامین گاز برای کوره: کوره بسیار داغ است، حدود ۲۰۰۰ درجه سانتیگراد. اما اگر دما خیلی بالا برود، بیش از ۶۰۰ تا ۸۰۰ درجه سانتیگراد، گرافیت شروع به تجزیه شدن میکند و آلودگی ایجاد میکند.
برای جلوگیری از این امر، از آرگون برای کنترل دما استفاده میشود. آرگون همچنین به جلوگیری از تلاطم هوا که میتواند باعث آسیب شود، کمک میکند. همزمان با جریان آرگون در کوره، ما از یک عنبیه برای کنترل میزان ورود و خروج آن استفاده میکنیم. حفظ جریان آرگون دقیقاً در محدودهی مناسب بسیار مهم است، بنابراین از تکنیکهای مختلفی برای انجام این کار استفاده میکنیم.
5. تصفیه هوا: سرعت پایین کشش مورد استفاده برای الیاف مخصوص به این معنی است که الیاف بدون پوشش معمولاً قبل از پوشش دادن توسط هوا خنک میشوند. کارخانههای بزرگتر تولید الیاف مخابراتی دارای بخشهای محصوری هستند که در آنجا گاز خنک میشود.
برخی شرکتها برجهای کشش را در اتاقهای تمیز (clean room) نیز راهاندازی میکنند. با این حال، اکثر تولیدکنندگان الیاف تخصصی از هوای پاک محیط - که با فیلترهای HEPA نصب شده در پشت پیشفرمها و کورهها و در بخشهایی از برج تمیز شده است - استفاده میکنند.
6. اندازهگیری قطر الیاف: قطر الیاف مخصوص از ۵۰ میکرون تا ۱۰۰۰ میکرون (۱ میلیمتر) متغیر است. اندازههای پرکاربرد شامل ۸۰، ۱۲۵ و ۴۰۰ میکرومتر هستند. قطر با سرعت کشش تعیین میشود. تغییرات کوچک در دمای کوره یا پیشساز، جریان گاز بیاثر یا سایر شرایط کشش میتواند باعث نوسانات کوچک در قطر الیاف شود.
برای جلوگیری از این وضعیت، برج دارای یک سیستم اندازهگیری مداوم است که دادهها را به حلقه کنترل قطر ارسال میکند. سرعت کشش مته را میتوان با استفاده از این اطلاعات تنظیم کرد. در برخی موارد، ممکن است یک حلقه کنترل ثانویه برای تنظیم تغذیه پیشساز وجود داشته باشد. این حلقههای کنترل از اندازهگیریهای قطر برای ایجاد تنظیمات سریع استفاده میکنند.
7. سیستم پوشش: پوشش فیبر برای محافظت از الیاف شیشه و حفظ استحکام آنها ضروری است. همچنین برخی از الیاف خاص وجود دارند که برای بهبود عملکرد نوری خود به پوشش نیاز دارند. اکثر پوششها دو لایه دارند: یک لایه داخلی نرمتر و یک لایه بیرونی سختتر که به شیشه متصل است.
این بدان معناست که سیستم پوشش باید دو رزین جداگانه را اعمال و عملآوری کند. فیبر وارد اولین قالب یا "فنجان" سیستم پوشش میشود که پوشش اولیه (لایه داخلی) را اعمال میکند. برخی از پوششهای ثانویه، به نام "رطوبتزدایی روی مرطوب"، میتوانند قبل از عملآوری پوشش اولیه اعمال شوند.
8. اندازهگیری متحدالمرکز: قطر فیبر و میزان تمرکز آن باید با استفاده از ابزارهای مبتنی بر لیزر اندازهگیری شود. نیروی مواد پوششدهنده به نگهداشتن فیبر در وسط قالب کمک میکند.
اگر مشکلی در تمرکز وجود داشته باشد، ممکن است لازم باشد فرآیند متوقف و دوباره شروع شود. داشتن پوشش صحیح روی فیبر برای جلوگیری از تلفات خمیدگی میکرو که میتواند باعث مشکلات تضعیف شود، بسیار مهم است.
9. چرخهای کپستان و تاپینگ: وینچ موجود در پایین پیش فرم، الیاف را از انتهای آن میکشد. همچنین سیستمی وجود دارد که الیاف را روی یک قرقرهی ذخیرهسازی میپیچد. کشش الیاف کنترل میشود تا از پیچیدن صحیح آن روی شفت جمعکننده اطمینان حاصل شود.
10. دستگاه تست و رولینگاستحکام کششی یک معیار کلیدی برای الیاف نهایی است. کارخانهها از این معیار برای یافتن مشکلات مربوط به پیشفرم و فرآیند کشش استفاده میکنند. دستگاه بازرسی دارای یک قرقرهی پرداخت، دو وینچ قابل کنترل و یک قرقرهی جمعکننده است.
دستگاه پروف معمولاً نزدیک وینچ اصلی برج کشش یا در یک اتاق جداگانه قرار دارد. برخی از تولیدکنندگان الیاف تخصصی، سیستمهای بازپیچی نیز دارند تا خروجی پیشفرم را به چندین رول - برای طول مشخص شده توسط مشتری الیاف - تقسیم کنند.
11. سایر تجهیزات برج کششی: برخی از انواع فیبرها برای کنترل ویژگیهای خاص خود به سیستمهای متفاوتی نیاز دارند. به عنوان مثال، فیبرهای با قطبش دایرهای و برخی دیگر از انواع فیبرها در طول فرآیند کشش نیاز به چرخش یا پیچاندن دارند.
این کار میتواند توسط دستگاه ریسندگی در سه نظام پیشساز یا دستگاه پیچاندن یا تکان دادن زیر آن انجام شود. کشیدن فیبرهای کریستال فوتونی با شکافهای هوا، حفرهها و سایر ویژگیها ممکن است به سیستمهای جریان گاز و فشار گاز اضافی برای کنترل فشار و رطوبت داخلی نیاز داشته باشد.
2. خط تولید بافر فشرده با کنترل HK-30 IPC+PLC
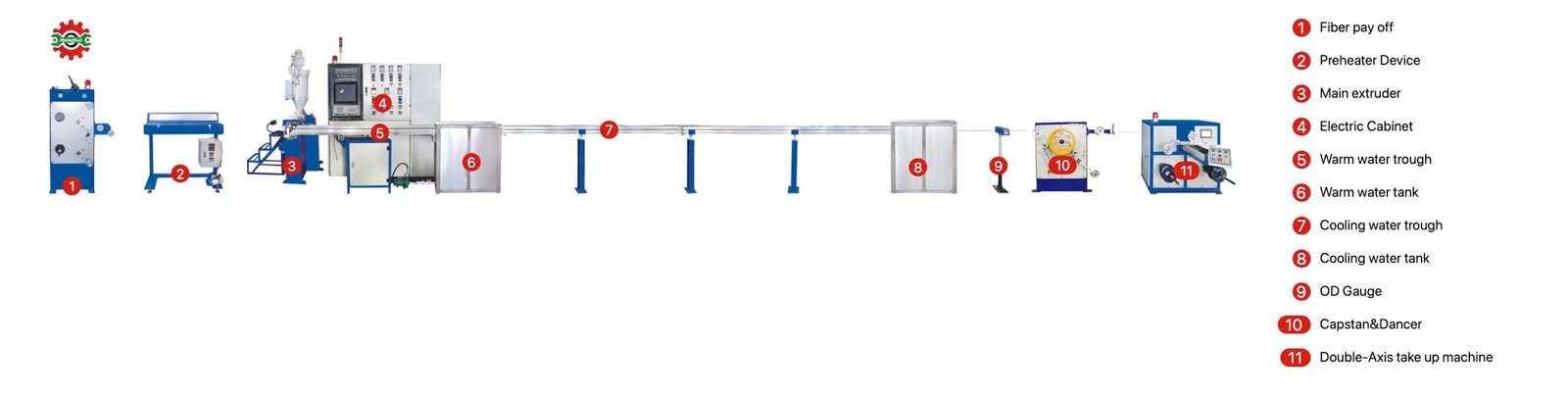
1. فیبر نتیجه میدهد: پوشیدن ۲۵ کیلومتر/۵۰ کیلومتر فیبر لخت.
2. دستگاه پیش گرمکن فیبر : گرم کردن فیبر قبل از اکسترودر.
3. اکسترودر اصلی: با استفاده از بهترین کیفیت پیچ از چین، اکستروژن پلی اتیلن/پی وی سی/TPEE ماده؛ موتور با استفاده از زیمنس به علاوه یک رمزگذار و از کنترل حلقه بسته استفاده میکند تا خط تولید برای تغییر قطر در طول افزایش یا کاهش سرعت خط پایدارتر باشد.
4. کابینت کنترل: کنترل PLC+IPC، کارکرد آسانتر برای کارگر، مبدل با استفاده از استاندارد آمریکایی امرسون/میتسوبیشی، ژاپنی، سایر قطعات الکتریکی با استفاده از اشنایدر.
5. آب گرم: استفاده از آب لوله کشی معمولی برای خنک کردن کابل
6. مخزن آب گرم: سینک را وصل کنید تا به طور خودکار آب گرم را دوباره پر کند.
7. آب خنک کنندهدمای آب حدود ۱۰ تا ۲۵ درجه سانتیگراد باشد تا قطر خارجی پایدار بماند.
8. مخزن آب خنک کننده: اتصال به دستگاه چیلر، پر کردن آب خنک کننده به آب خنک کننده از طریق خودکار
9. گیج OD: قطر واقعی کابل را به اپراتور نمایش میدهد.
10. کاپستان: تغییر خودکار سرعت خط توسط پاناسونیک سروو پلاس گیربکس.
11.برداشتن: استفاده از موتور زیمنس، عبور از سروو و همچنین یک صفحه نمایش برای افزایش/کاهش سرعت اپراتور وجود دارد.
جهان نهایی
اگر به این پروژه علاقهمند هستید، بیایید با شما تماس بگیریدبرای دریافت پیشنهاد